Erecting traditional buildings follows a sequential process. Each step is dependent on the completion of the previous section, from foundations to building frames, walls, and roofing. With several components involved, the construction process unsurprisingly faces many potential bottlenecks.
But that’s not all. Harsh weather conditions and a shortage of skilled workers can drag construction times further. Managers often need to perform extensive on-site design revisions and specialized labor. The solution? Pre-engineered fabric buildings. These structures, also called tensioned fabric buildings, can be used in a wide range of applications.
Let’s find out why you must consider them in your next project.
Eliminates Several Processes With Its Streamlined Design
Pre-engineered fabric buildings are assembled from pre-made components, including the fabric membranes and steel frame systems, that enable rapid construction. Fabric buildings are manufactured even before arriving on the project site. Off-site manufacturing shortens the labor and preparation required for initial site work. For example, you don’t have to wait for concrete to ‘cure’, which could take several days to achieve maximum strength. There are also fewer parts to build and assemble, which significantly cuts construction time.
These modern building solutions have standardized designs and components based on industry standards. However, they also offer design flexibility, as fabric building manufacturers can customize them to different sizes, shapes, and functionalities.
Industrial applications for pre-engineered fabric buildings include warehouses, storage areas, sports facilities, and temporary shelters. Business owners can also use their less versatile cousins, tension fabric structures, as event spaces or architectural additions to buildings.
Minimal Foundation Requirements and On-Site Assembly
It takes several months to more than a year to construct an average-sized building using traditional construction methods. Laying a foundation alone could take up to four weeks. Comparatively, most fabric shelters take only a few hours or days to complete. That’s because you don’t need to excavate and level the ground to make a foundation.
You can use concrete slabs, ballast blocks, and helical anchors to build your structure on. Some manufacturers even offer foundation-free options. Regardless, you need a proper anchoring system to guarantee stability and structural integrity.
These building structures follow a modular design, allowing teams to easily connect the pre-assembled components without additional effort. Construction teams don’t have to waste time correcting potential errors as the fabric buildings’ pre-engineered components are built and fabricated to fit each other. Pre-engineered fabric building kits come with instructions so your team can easily bolt and fasten structural parts. Once done, all that’s left to do is to ‘tension’ the fabric cover over the steel frames.
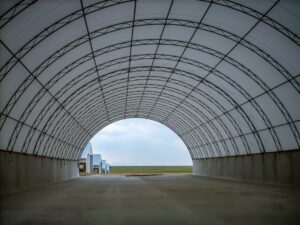
Reduces Labor Needs and Facilitates Immediate Usability
Traditional construction requires project managers to hire skilled tradespersons, including welders, roofers, carpenters, and masons. Assembling a capable team can be a challenge especially as the construction industry grapples with a serious labor shortage. Extreme weather conditions can negatively impact efficiency, as they cause further delays and force your specialized crew to work longer.
Unlike traditional structures, fabric buildings don’t require complex construction work. You don’t have to install roofing or build walls, so you’ll save time and labor. A small team of general construction workers and a few supervisors is enough to assemble these fabric structures and extend your usable space.
Conventional buildings require extensive drying and curing times and finishing before you can start occupying them. In comparison, you can use fabric buildings right away once they’re up. They provide perfect solutions to a wide variety of industries requiring rapid deployment and expansion.
Apart from quick installation, pre-engineered fabric systems are easy to dismantle and reassemble. But don’t confuse easy with weak. Portable fabric buildings can withstand North America’s harsh environmental loads and corrosive environments, making them perfect for use as military shelter systems or a manufacturing facility.
Cost-Efficiency
Pre-engineered fabric buildings promote cost efficiency by minimizing resource and material requirements. These structures don’t require a huge construction team, and assembly time only takes a few days or weeks, depending on the size and configuration.
As they come pre-assembled, builders don’t need to cut materials on-site, eliminating construction waste and energy costs. The building’s fabric material also allows natural light to enter during the day, reducing your lighting costs in the long run.
It also allows for flexibility as your needs change. For example, you can add more modules if you need extra space or want to optimize office areas. The best part is that teams can revise these configurations without starting from scratch or requiring extensive changes in design and construction flow.
Closing Thoughts
Pre-engineered fabric structures are reshaping the construction industry and a vast range of industries that demand instant shelter solutions. These modern building options alter the speed of construction by allowing off-site fabrication and simplifying on-site assembly and eliminating the need for extensive resources.
Cutting off months of construction work means organizations can achieve their operational goals faster, further minimizing costly downtime. This adaptability means a lot for business owners seeking to save on material costs without affecting sales potential.